自动驾驶让整车厂和芯片厂商摩擦升级?
通常情况下,智能手机或服务器中的这些问题都会在若干年内通过包括软件更新在内的诸多方法得到解决,自动驾驶汽车也可能复制这种路径。不过,目前整个汽车行业正在全力以赴追赶或超越特斯拉,唯一的超车方式就是使用电子产品。
“可靠性的典型学习周期是一年两次,”PDF Solutions新产品和解决方案副总裁Klaus Schuegraf说。 “首先,你需要制造出来产品,这需要两到四个月的时间,然后封装它,给它烧录软件,这又需要一个季度。所以,从开始制造到烧录软件需要历时半年,你每年大约会经历两次学习周期。这是将这些高性能、高可靠性技术推向市场以实现高性能计算的一部分挑战。你可能会遇到一两个ppm故障率问题,使得无法提供和先前节点一样的质量。这些故障都延长了处理时间,当然,发现这些难题并定位它们也需要时间。”
生产中的变化也是导致可能出错的一个原因。
“你当然可以保证生产质量,但实现起来非常困难,”联华电子营销总监John Chen说。 “和8英寸晶圆相比,12英寸晶圆将在中心提供更好的均匀性,但在晶圆边缘比8英寸晶圆更加难以保持均匀性。所以你可以改回200mm晶圆,以降低故障率并最大限度地减少产品变化。问题在于你不一定知道如何将其用于汽车行业,有时你必须在工艺上向后退一步而不是转向最先进的节点。”
所有人都在关注AI
在辅助驾驶和自主驾驶汽车领域,最受关注的一个热点是如何让汽车通过意料之中和意料之外的障碍,适应不断变化的道路状况,满足不同的交通规则。由于汽车行业的设计周期较长,为了避免过时,汽车制造商现在正在研究7nm AI芯片。此外,他们还在考量各种封装方案,比如多芯片模块以及22,18,12nm的FD-SOI。他们正在权衡需要把多少逻辑集中到一起,为了尽量避免数据传输,可以在更接近传感器的位置进行多少处理。
无论采用什么样的方法,都有许多变量和移动部件使得很难收集到足够的数据。
“你认为车内的人工智能器件温度都得到了良好控制,”三星代工营销高级总监Bob Stear表示。“但是,更多的智能应该在终端节点上实现。我们现在正在对汽车进行特征化,现在面向汽车芯片有28nm和18nm FD-SOI,和‘1级合格’的14nm,预计到今年年底还会提供7nm。”
工艺只是控制温度的一个手段。其它因素还包括内存,温度也和这些芯片的封装形式有关,封装对温度的影响可能会成为一个独立的问题。
格罗方德产品线管理高级主管Jamie Schaeffer表示:“我们已经发现,当你在一个MCU上堆叠NVM时,封装的接口会在高温下失效。这里的关键要求之一是存储器和嵌入式MRAM必须能够承受150°C的结温,这个温度满足汽车级别1。”(汽车级别0需要在175°C下认证。)
现在的问题是,用于自动驾驶汽车的AI芯片并没有唯一的最佳架构或制造方案,也没有公认的将传感器封装在一起,或者确定哪些数据该在哪里的最佳方法。而且,关于哪里才是汽车边缘,每个架构之间以及每个制造商之间也没有统一的概念。
还缺少什么?
那么,汽车OEM和半导体制造商这两个世界该如何充分链接?一种方法是交叉教育,不论需要耗费多少时间,这种方法都是必须的。
Coventor首席技术官David Fried说,“大概30多年前,我们经历了一次演变,当时可不是现在这种无晶圆厂的情况。那时候,每家公司都制造自己设计的产品,然后我们变革了半导体行业,走向无晶圆厂和代工厂模式。一切都朝着不同的方向发展了。无晶圆厂的人说,他们甚至都不想知道晶圆厂到底是怎么样制造他们设计的芯片的。‘你只需要给我设计规则,我设计好它,就应该有较高的良率,如果做不到,那就是你们晶圆厂的问题。’可是现在情况变得更加复杂了,无晶圆厂和代工厂的边界越来越小了。现在无晶圆厂的人必须了解晶圆厂中发生的许多事情,他们已经接受了这一点而且希望这么做。从某种程度上来说,半导体行业正以这种方式重新聚合在一起。当然,这些无晶圆厂公司购买或建造晶圆厂的情况未必出现,但是他们已经开始走到了一起。有些硅片生产专家现在在无晶圆厂设计公司工作,因为无晶圆厂公司必须知道芯片是怎样制造出来的,才会拿出更好的设计,让他们的产品更好地发挥作用。”
Fried并不是唯一看到这种趋势的人。事实上,从设计前端到后端制造,人们都慢慢达成了共识。
“这毕竟是两个不同的专业知识领域,”Synopsys汽车战略副总裁Burkhard Huhnke表示。“从本质上来说,汽车仍然是以机械科学为主导的行业。但是现在,突然一切都电动化了,你需要逆变器、IGBT等高压元件,你需要模拟一切瞬态特性,这些东西可能是汽车公司未来的核心竞争力。不过现在,这种变化才刚刚开始,智能手机行业和其它临近行业的许多新人正在进入汽车领域。”
不过,我们需要以不同于半导体行业的方式看待从设计到制造整个链条的汽车供应链。
“汽车行业之前遵循的是一种瀑布模型,”弗劳恩霍夫自适应系统部工程设计方法部门主管Roland Jancke说。“汽车制造商会向博世或者海拉这样的一级供应商提供技术规格,这些一级供应商设计并生产安全气囊或电机控制系统这些汽车上的系统。一级供应商选择二级供应商,比如哪个提供芯片,那么提供阻容等。每一级供应商都会把技术规格提供给下一级,决定如何划分系统,并给子系统提供更深一层的规范。但是现在这个模型不再奏效了,因为它传导得太慢了,而且链条上给出的信息确实不够。这个传导链条太长,有些信息也没有反馈上来。因此,汽车制造商并不完全了解他们当他们想了解汽车中的某些技术时会得到哪些信息。”
另一方面,汽车公司需要了解模拟时数据是怎么使用的,需要依赖使得半导体行业蓬勃发展的各种数据。
ANSYS的首席技术专家JoaoGeada说:“当有现实世界的数据时,并非所有数据都是被模拟出来的。还有一些来自强制老化的数据,强制老化是指将芯片/设计处于极端条件(高温、高电压、快速工艺角)下测试,并延长时间以最大化老化效应。它们提供了一些验证模拟数据的真实数据。我们(EDA)在模拟方面做得非常好,非常准确。一旦有一些数据点能够确认模拟结果可以匹配上观测结果,人们就会相信模拟的力量。”
然而,这些对汽车行业来说都是新课题,而且在某些领域并不存在和所有这些电子系统相关的标准。
“是有一些标准,如JEDEC标准、ISA规范、IEEE标准,”Fraunhofer的Jancke说。“但其中一些是在30年前确定的。在功能安全域中,您需要为这些标准设置组件的故障率。但是这些供应商提供的故障率来自大约30年前建立起来的表格,因此它们不再有效或不再有意义了。这些标准需要进行改进,以适应我们现在的技术。”
结论
上面这些方法最终如何融合到一起,现在还很难判断。不过它们足够让车辆中很多功能电动化,更不用说让它们在可接受的参数范围内运行了。数据将是决定这种进展的关键要素,但是进展速度有多快,向哪个方向发展目前还不完全清楚。
“几十年来,汽车行业一直在获取IC的可靠性数据,”西门子子公司Mentor总裁兼首席执行官Wally Rhines表示。“但是焊球、凸块以及其他类型的制造数据仍然相当有限,因为出货单位和包含先进封装的设计仍然很少。工业和制造业需要足够的数据点来保证质量和可靠性,但他们需要的数据量可能与过去不同。我们仍处于对所有这些数据进行分类的阶段。”
这个阶段何时完成,所有这些不同世界整合起来后会是什么样子,这些答案依然只能存在于人们的猜测中。
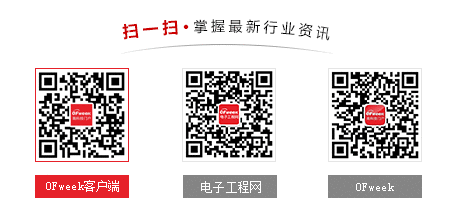
图片新闻
技术文库
最新活动更多
-
1月8日火热报名中>> Allegro助力汽车电气化和底盘解决方案优化在线研讨会
-
1月9日立即预约>>> 【直播】ADI电能计量方案:新一代直流表、EV充电器和S级电能表
-
即日-1.16立即报名>>> 【在线会议】ImSym 开启全流程成像仿真时代
-
即日-1.20限时下载>>> 爱德克(IDEC)设备及工业现场安全解决方案
-
即日-1.24立即参与>>> 【限时免费】安森美:Treo 平台带来出色的精密模拟
-
即日--2.7了解详情>> 【森海塞尔】TeamConnect系列产品——提升视听之体验,塑造音频之未来
推荐专题
发表评论
请输入评论内容...
请输入评论/评论长度6~500个字
暂无评论
暂无评论