元器件布局不合理对可制性的影响
元器件在PCB上的正确安装布局是降低焊接缺陷的极重要一环。元器件布局时,应尽量远离挠度很大的区域和高应力区,分布应尽可能均匀,特别是对热容量较大的元器件,应尽量避免采用过大尺寸的PCB,以防止翘曲。布局设计不良将直接影响PCB的可生产性和可靠性。
1、布局设计不良
①如图1(a)所示,磁珠的高度高于下面的绝缘片高度,用螺钉将绝缘垫片固定在PCB上时,力度稍有偏大,便会造成磁珠破裂。
②如图1(b)所示,PBGA 17mm×15mm共4只,分别在A面和B面完全对称放置,返修时难以控制上、下两面BGA的焊球焊接工艺。
图1 磁珠的高度高于绝缘片高度的PCB布局及A、B两面BGA镜向设计
③靠近板边的系列插针距离板边距离不足1mm,而此边为V-CUT拼板处,影响V槽机器自动分板,如图2(a)所示。
④A面的D32/D35的引脚被包含在B面元器件X2的丝印框内,造成生产中由于过波峰焊B面需要贴胶纸,挡住了D32/D35的引脚,如图2(b)所示。
图2 导致无法自动分板和增加焊接保护工序的布局设计
⑤使用工艺流程为B面点胶固定片式元器件→插装A面元器件→过波峰焊。但B面的D3元器件本体下方有长槽腰孔,无法对该元器件进行点胶固定,只能采取手工焊接D3,如图3(a)所示。
⑥发光二极管(HL31、HL32、HL34、HL35)的引脚方向与面板垂直,插装后没有办法装入面板中,需将灯的焊盘及丝印旋转90°,如3(b)所示。
图3 无法进行自动焊接的布局设计
⑥PCBA上装有8个连接器,每个连接器有168个引脚,工艺流程为双面回流焊后手工焊,手工焊接时间太长,焊点多且烙铁头无法完全伸入焊接,严重影响产品质量和生产时间效率,如图4所示。
图4 需要手工焊的布局设计
⑦PCB上、下质量和密度分布不均匀,导致单板加工时变形等缺陷,如图5所示。
图5 质量和密度分布不均匀
2、应用波峰焊工艺时,元器件布局没有采取克服“阴影效应”措施
①表面张力和元器件体造成的“阴影效应”,如图6(a)所示。
②延长焊盘克服“阴影效应”,如图6(b)所示。
图6 波峰焊时的“阴影效应”及正确设计
3、元器件的排布不符合工艺要求
采用回流焊和波峰焊工艺时不同的元器件布局设计如图7所示。
①采用回流焊工艺时,元器件的排布方向应与PCB进入回流焊炉的方向一致。
②采用波峰焊工艺时,应考虑波峰焊阴影效应。
图7 采用回流焊和波峰焊工艺时不同的元器件布局设计
4、安放在PCB焊接面的QFP和SOIP没有设计成“菱形”和设计导流盘
①QFP等封装不建仪采用波峰焊接。
②如需采用波峰焊接,则按图8所示设计。
图8 采用波峰焊接工艺时QFP的菱形布局设计
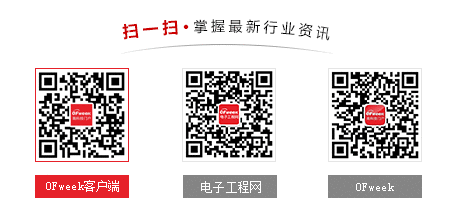
图片新闻
技术文库
最新活动更多
-
1月8日火热报名中>> Allegro助力汽车电气化和底盘解决方案优化在线研讨会
-
1月9日立即预约>>> 【直播】ADI电能计量方案:新一代直流表、EV充电器和S级电能表
-
即日-1.16立即报名>>> 【在线会议】ImSym 开启全流程成像仿真时代
-
即日-1.20限时下载>>> 爱德克(IDEC)设备及工业现场安全解决方案
-
即日-1.24立即参与>>> 【限时免费】安森美:Treo 平台带来出色的精密模拟
-
即日-1.31立即参与>>> 【限时免费下载】村田白皮书
推荐专题
发表评论
请输入评论内容...
请输入评论/评论长度6~500个字
暂无评论
暂无评论