印制板(PCB)的工艺选型
五、PCB表面处理工艺简介
PCB表面处理最基本的目的是保证良好的可焊性或电性能。由于铜在空气中很容易被氧化,而铜的氧化层对焊接有很大的影响,如果铜层被氧化则很容易造成假焊、虚焊,严重时会造成焊盘与元器件无法焊接,虽然可以采用强助焊剂除去大多数铜的氧化物,但强助焊剂本身的残留也会给产品带来腐蚀。因此业内普遍的处理方式是在PCB生产制造时增加一道工序,即在焊盘表面涂覆(镀)上一层物质,保护焊盘不被氧化。
目前国内的PCB表面处理工艺有:喷锡(Hot Air Solder Leveling,HASL热风整平)、OSP(防氧化)、全板镀镍金、沉金、沉锡、沉银、化学镍钯金、电镀硬金,某些特殊应用场合还会有一些特殊的PCB表面处理工艺。下面进行简要介绍。
(1)热风整平(喷锡)
热风整平又名热风焊料整平(俗称喷锡),它是在PCB表面涂覆熔融锡(铅)焊料并用加热压缩空气整(吹)平的工艺,以形成一层既抗铜氧化又可提供良好的可焊性的镀层。热风整平时焊料和铜在结合处形成铜锡金属间化合物。PCB进行热风整平时要沉在熔融的焊料中,风刀在焊料凝固之前吹平液态的焊料,风刀能够将铜面上焊料的弯月状最小化并阻止焊料桥接。热风整平分为垂直式和水平式两种,一般认为水平式较好,其镀层比较均匀,且便于实现自动化生产。
① HASL工艺的优点是:价格较低,焊接性能佳。
② HASL工艺的缺点是:不适合用来焊接细间隙的引脚及过小的元器件,因为喷锡板的表面平整度较差,且在后续组装过程中容易产生锡珠(solder bead),对细间隙引脚(fine pitch)元器件较易造成短路。
(2)有机可焊性保护剂(OSP)工艺
有机可焊性保护剂工艺是PCB铜箔表面处理的符合RoHS指令要求的一种工艺。世界范围内,目前有25%~30%的PCB使用OSP工艺,且该比例还在持续上升。OSP工艺可以用在低技术含量的PCB上,也可以用在高技术含量的PCB上,如单面电视机用PCB、高密度芯片封装用PCB。对于含BGA器件的PCB,OSP应用也较多。事实上,对于没有表面连接功能性要求或储存期限定的应用场合,OSP工艺将是最理想的表面处理工艺。
① OSP工艺的优点是:制程简单,表面非常平整,适合无铅焊接和SMT。
② OSP工艺的缺点是:焊接时需要氮气,且回流焊次数受限(多次焊接会导致膜被破坏,2次没有问题),不适合压接技术,不适合返修且存储条件要求高。
(3)全板镀镍金
全板镀镍金是在PCB表面导体上先镀一层镍再镀一层金,镀镍主要是为了防止金和铜间的扩散。目前电镀镍金主要有两类:镀软金(纯金,表面看起来不亮)和镀硬金(表面平滑且坚硬,耐磨,含有钴等其他元素,表面看起来较光亮)。软金主要用于芯片封装时打金线,硬金主要用在非焊接处的电性互连。
① 镀金工艺的优点是:较长的存储时间(>12个月),适合接触开关设计和金线邦定,适合电测试。
② 镀金工艺的缺点是:较高的成本,金比较厚且金层厚度一致性差,焊接过程中,可能因金太厚而导致焊点脆化,影响强度。
(4)化学镀镍/浸金(ENIG)
化学镀镍/浸金也叫沉金,是在铜面上包裹一层厚厚的、电性良好的镍合金,这可以长期保护PCB。ENIG具有其他表面处理工艺所不具备的对环境的忍耐性,此外沉金也可以阻止铜的溶解,这将有益于无铅组装。
① ENIG工艺的优点是:不易氧化,可长时间存放,表面平整,适合用于焊接细间隙引脚及焊点较小的元器件,可耐受多次回流焊,适合返修,适合用作COB(Chip On Board)打线的基材。
② ENIG工艺的缺点是:成本较高,焊接强度较差,容易产生黑盘问题,镍层会随时间逐渐氧化,长期可靠性不良。
(5)其他表面处理工艺
其他表面处理工艺还包括沉锡工艺、沉银工艺、化学镍钯金和电镀硬金等。
① 沉锡工艺:由于与焊料的良好兼容性,使其具有良好的可焊性,同时其平整度优良,适合无铅焊接和压接;缺点是不耐存储。焊接过程最好有N2保护,且容易产生“锡须”。
② 沉银工艺:介于有机涂覆和化学镀镍/沉金之间,工艺比较简单,即使暴露在热、湿和有污染的环境中,银仍然能够保持良好的可焊性;缺点是不具备化学镀镍/沉金所具有的好的物理强度,存储条件要求高,易污染,易氧化,同时焊接强度不好,易出现微空洞问题。
③ 化学镍钯金:较沉金在镍和金之间多了一层钯,从而具有更好的抗腐蚀性,抵抗环境攻击性强,适合长时间存储,适用于无铅焊接、厚板和开关接触设计等。
④ 电镀硬金:常用于对耐磨性能要求高的电连接器“接触对”中。
六、PCB工艺选型要求
6.1 基材选择
印制板的基材直接影响印制板的基本性能、制造工艺和成本,选用时应进行综合考虑。除应满足电子产品电气性能、机械性能的要求外,还应同时考虑印制板在后续组装生产中的性能要求,即能否经受住电子产品装联整个工艺过程(包括回流焊、波峰焊、压接、返修、清洗、三防涂覆等工序)中的热应力和机械应力考验,特别是波峰焊和回流焊过程的热冲击对基材的考验最大。
不同基材的性能和成本差异较大,选用时应结合产品的性能特点进行选择,以满足要求为原则,切勿盲目追求高性能、高价格。一般通信类产品印制板应满足2级以上要求,高可靠产品应满足3级要求,SMT印制板应选择高Tg(玻璃化转变温度)的材料,至少要高于印制板的工作温度(140℃),同时应选择耐热性能好的材料(260℃,保持50s)。目前电子产品中广泛使用的是以减成法(铜箔蚀刻法)制造印制板时所采用的覆铜箔层压板(简称覆铜板),它也是目前国内外使用量最大的印制板基材。
PCB基材选用要素及说明如表3所示。
表3
6.2 厚度选择
印制板的厚度应满足产品对其机械强度的要求,此外,还应根据其外形尺寸、层数、所安装元器件的质量、安装方式等进行综合考虑。
① 一般优选标准厚度的基材,慎选非标基材,对于非标基材的选择,要经过严格评估和验证。印制板的标准厚度为0.70mm、0.80mm、0.95mm、1.0mm、1.27mm、1.50mm、1.60mm、2.0mm、2.4mm、3.0mm、3.2mm、3.5mm、4.0mm、6.4mm。
② 在能满足安全使用的前提下,优选厚度较薄的基材,以减轻产品质量和降低成本。
③ 当安装的元器件质量较大或振动负荷较强时,应采取缩小印制板尺寸、加固或增加支撑点等措施避免印制板变形。
④ 板面较大或无法加固、支撑时,应适当增加板厚,在不考虑其他影响因素的情况下,把宽厚比控制在150以下最为理想。
⑤ 对于有印制插头的印制板,应根据与连接器匹配的要求确定板的厚度和公差,过厚的板会造成插拔困难;过薄的板会引起接触不良。
⑥ 对于有VPX等压接连接器的印制板,厚度和焊盘孔设计应严格遵照连接器使用要求执行。
⑦ 对于挠性板,当使用附加镀(涂)覆层、覆盖层或胶黏剂时,板的总厚度会大于挠性覆铜箔基材的厚度,因此对其尺寸公差要求应尽可能宽松。
常见PCB板材厚度及选择,如表4所示。
表4
常见板材铜箔厚度及选择如表5所示。
表5
6.3 镀层选择
印制板镀层应根据产品的性能要求和成本控制要求进行选择,还应考虑焊盘表面处理工艺的成熟度、稳定性、环境适应性和所安装元器件的机械承载要求。
① 热风整平工艺对于控制镀层的厚度和焊盘图形较为困难,不推荐使用在含有0.4mm细间距元器件和1.0mm间距以下BGA的PCB中,原因是细间距元器件对焊盘平整度要求较高,而热风整平工艺的热冲击可能会导致PCB翘曲。
② 对于有压接型电连接器的产品、需要回流或返修的产品及工艺制程中不能提供氮气保护的情况,都不推荐选用有机保护层OSP。
③ 对于需要较高焊接强度的高可靠性产品,限制使用沉金镀层和沉银镀层。
④ 对于需要电测的产品,限制使用沉银镀层、沉锡镀层和OSP镀层。
⑤ 对于有金线邦定的产品,优选热风整平镀层、全板镀镍金镀层和化学镍钯金镀层。
6.4 结构/层数选择
印制板的结构和层数选择应以满足产品性能要求为前提,还应综合考虑产品的布线密度要求、整机给予印制板的空间尺寸和电气性能要求等。
① 印制板的结构主要根据产品的结构形式、空间大小和互连要求选择。
② 从可靠性和可制造性的角度考虑,优先选择单面板、双面板设计,其次是多层板。
③ 多层板设计中,优先考虑四层板、六层板的设计。
④ 若采用双面板时布线密度很大,则建议采用布线密度较小的多层板。
⑤ 从电磁兼容性角度考虑,当时钟电路的频率超过5MHz或上升时间小于5ns时,优先选择多层板(即5/5规则)。
6.5 外形及尺寸选择
印制板的外形及尺寸应根据其在整机中的安装尺寸和布线密度要求选择,并应综合考虑机械强度、设备要求和美观性等。
① 在满足整机空间布局要求的前提下,外形力求简单,一般为长宽比例不太悬殊的长方形,最佳长宽比参考为3∶2或4∶3,也允许有圆形和其他异形。
② 对于长宽比例较大或面积较大的印制板,容易产生翘曲变形,需要增加板的厚度或采取增加支撑点和边框加固等措施。
③ PCB的外形优选矩形的(四角为R=1~2mm,圆角更好,但不做严格要求)。偏离这种形状会引起PCB传送不稳、插件时翻板和波峰焊时熔融焊料溅起等问题。
④ 对于不规则形状的印制板,设计时应考虑采用工艺拼板的方式将其转换为矩形,特别是角部缺口一定要补齐。
⑤ 印制板的结构尺寸(包括外形与孔位)应与电控盒的机械结构设计完全匹配。螺丝孔半径2.5mm内不能有铜箔(除要求接地外)及元器件(或按结构图要求)。
⑥ 印制板的最大尺寸范围:不应超过设备极限尺寸,一般情况下,用于SMT的PCB应小于460mm×460mm,用于波峰焊的PCB应小于508mm(使用托盘的情况下,则不能超过450mm)。
⑦ 印制板的最小尺寸范围:应考虑便于生产的原则,一般情况下,当PCB长边尺寸小于125mm、短边小于100mm时,应通过拼板转换为理想尺寸,以便插件和焊接。
⑧ 当印制板边缘5mm范围内必须有电路图形或焊盘时,应设计工艺夹持边,工艺夹持边内不应有焊盘图形,其宽度一般取3.8~10mm。
⑨ 对于需要进行测试的印制板,应留有测试工装的定位孔,定位孔与板边缘至少有2mm以上的间距,保证针床、测试工装等的方便使用。
6.6 平整度要求
根据电子产品规模化高效生产的需要,现代电子组装越来越依赖自动化生产设备,自动化生产对印制板表面的平整度也提出了更高的要求。印制板平整度不良主要表现为翘曲,通常包含弓曲和扭曲两种变形。翘曲对组装的合格率和可靠性的影响很大,容易引发组装过程中的引脚偏移、虚焊等问题。翘曲产生的内应力容易导致焊点开裂、失效,有时甚至会损坏生产设备,因此印制板的翘曲问题引起了电子组装厂商的广泛重视。
造成印制板翘曲的因素很多,有材料本身的质量问题、材料选用问题、单板叠层设计问题,也有工艺制程问题等。IPC给出了印制板翘曲度的可接受标准:用于表面贴装的印制板允许最大翘曲和扭曲为0.75%,其他各种板子允许1.5%。
实际生产中,目前国内外电子装配厂许可的印制板翘曲度标准一般为0.7%~0.75%,部分电子厂甚至提高到了0.3%;用于波峰焊的印制板对平整度的要求一般为翘曲度小于0.5mm,如果大于0.5mm则应进行整平处理。对于板厚在1.6mm以下的印制板,翘曲度还应更小。
6.7 尺寸公差要求
印制板应满足设计图纸规定的尺寸要求,但由于制造不准确或出于满足结构配合的要求,实际制造中会存在尺寸公差,加工PCB时应严格将其控制在公差允许范围内,避免影响后续装配和焊接。
(1)外形尺寸公差
外形尺寸涉及焊接和装配问题,现代电子产品设计布局越来越精密,对产品外形尺寸精度的要求越来越高,但受制于设备能力,目前PCB工厂公差控制能力并不能完全适应产品对公差的严格需求,因此在产品结构设计时应充分了解PCB工厂的实际加工能力。
目前,主流板厂印制板外形尺寸极限偏差如表6所示。
表6
(2)厚度尺寸公差
PCB厚度受制于基板材料本身公差、工厂加工能力、产品设计残铜率、材料胀缩等多种因素,很难精确控制,因此在产品结构布局时更应充分考虑到板厂公差能力,预留足够的设计余量。
目前,主流板厂多层板厚度尺寸极限偏差(成品板)如表7所示。
表7
注:成品板厚度=基材厚度+铜材厚度+表面镀层厚度+阻焊层厚度。
(3)孔径尺寸公差
PCB孔径尺寸公差主要影响插件的安装。由于PCB的高集成度要求,各种高密度插接元器件开始应用在单板上,给PCB孔径公差控制提出了更加严格的要求。在PCB设计时应密切关注PCB厂家控制孔径公差的能力,避免出现后续组装问题。
目前,主流板厂印制板厚度尺寸极限偏差(成品板)如表8所示。
表8
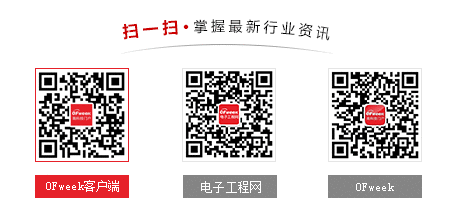
图片新闻
技术文库
最新活动更多
-
即日-12.26立即报名>>> 【在线会议】村田用于AR/VR设计开发解决方案
-
1月8日火热报名中>> Allegro助力汽车电气化和底盘解决方案优化在线研讨会
-
1月9日立即预约>>> 【直播】ADI电能计量方案:新一代直流表、EV充电器和S级电能表
-
即日-1.14火热报名中>> OFweek2025中国智造CIO在线峰会
-
即日-1.16立即报名>>> 【在线会议】ImSym 开启全流程成像仿真时代
-
即日-1.20限时下载>>> 爱德克(IDEC)设备及工业现场安全解决方案
推荐专题
发表评论
请输入评论内容...
请输入评论/评论长度6~500个字
暂无评论
暂无评论