半导体的3D时代
Logic
对于3D NAND“节点”,可以轻松地根据物理层数进行定义,对于DRAM节点一般采用有源区的半节距,而逻辑节点几乎是公司营销人员称之为多少就是多少。
由于FinFET是3D结构,因此某些人认为当前的FinFET前沿工艺是3D,但在本次讨论中,我们认为3D是指器件堆叠,即允许堆叠多个有源层以创建器件堆叠的情况。在这种情况下,一旦采用CFET,3D逻辑器件将真正出现。图7列出了追求最新技术的3家公司的节点路线图。
图7.逻辑路线图。
由于英特尔与代工厂之间的分裂,此图中的节点比较变得复杂。英特尔遵循经典的节点名称,即45nm,32nm,22nm,14nm,而代工厂遵循的是“新”节点名称,分别为40nm,28nm,20nm,14nm。此外,英特尔在每个节点上微缩更多,因此Intel 14nm的密度与代工厂10nm类似,Intel 10nm的密度与代工厂7nm类似。
在图的顶部,我概述了基于交替的0.71和0.70倍微缩得到的节点名称系列。在图的底部,我按公司和年份列出了每个节点的晶体管密度。如前所述,晶体管密度是基于NAND和Flipflop单元的权重计算的。括号中每个节点的旁边是FF(FinFET),HNS(水平纳米片),HNS / FS(Forksheet,基于Imec的工作来提高密度)和CFET(互补堆叠的FET,其中nFET和pFET是垂直堆叠)。CFET量产之时,就是逻辑微缩从基于单层的微缩成为真正的3D解决方案之日,原则上CFET可以通过添加更多层来继续进行微缩。
图中粗体表示领先的密度或技术。2014年,英特尔凭借其14纳米工艺在密度上取得了领先地位。台积电在2016年以10纳米制程占据密度领先地位,并在2017年以7纳米制程保持领先地位。台积电和三星在7nm处的密度相似,但要达到5nm,台积电的微缩率要比三星大得多,2019年,台积电以其5nm技术保持工艺密度领先。如果三星在2020年实现HNS技术(我们称之为3.5纳米节点),那么他们可能会在密度上领先,并成为第一家制造HNS的公司。在2021年,TSMC的3.5纳米节点(我们称之为)可能会帮助他们返回到密度领先位置。如果英特尔能够实现他们通常目标的那种两年一次微缩的速度,我们相信他们可以在2023年在采用5纳米工艺时重新取得密度方面的领先。
图8给出了这些逻辑制程的掩模数量。EUV的引入减少了掩模数,如果没有EUV,我们可能会在此图表上看到100个以上的掩模。正如我们对NAND掩膜计数图所做的那样,虚线是平均掩膜数。我们还基于“相似”密度对工艺进行了分组,例如,将Intel 14nm与代工厂10nm工艺结合在一起,将Intel 10nm与代工厂7nm工艺结合在一起。
图8逻辑制程掩模数趋势。
图9显示了基于前面提到的NAND /D触发器加权度量的每平方毫米晶体管的逻辑密度。
图9.逻辑密度趋势。
此图表上绘制了六种类型的制程。直到2014年左右,平面晶体管还是主要的前沿逻辑工艺,其密度每年提高1.33倍,FinFET接管了前沿技术,密度每年提高1.29倍。与FinFET并行,我们已经看到了FDSOI工艺的引入。FDSOI提供了更简单的工艺,更低的设计成本以及更好的模拟,RF和功耗,但无法与FinFET竞争密度或原始性能。当HNS从FinFET接管后,我们预计密度的提高速度将进一步放缓至每年1.16倍,最终CFET将接管并以每年1.11倍的速度增加密度。我们还根据IMEC的工作绘制了由垂直晶体管生产的SRAM,这些SRAM可能为高速缓存chiplet提供有效的解决方案。
图10展示了逻辑晶体管成本的趋势。
图10.逻辑晶体管成本。
图10通过将我们的战略成本和价格模型中的晶圆成本估算值与图9中的晶体管密度相结合,得出了每十亿个晶体管的成本。所有晶圆厂都是新建的工厂,每月产能为35,000片晶圆,因为这是将在2020年建成的逻辑晶圆厂的平均产能。晶圆厂与国家/地区对应关系为,GLOBALFOUNDRIES-德国(除14nm在美国),英特尔-美国(除以色列的10nm芯片),台积电-台湾,三星-韩国。
该图不包括掩模组或设计成本摊销,因此,在降低每个晶体管的制造成本的同时,能够使用这些技术的设计数量仅限于大批量产品。该图不包括任何封装测试或良率影响。
从130纳米降低到i32 / f28(英特尔32纳米/代工厂28纳米)每节点成本下降0.6倍,然后从i22 / f20到f16 / f14节点,由于代工厂决定为了FinFET而不微缩太多,成本降低速度减慢了。这种放缓导致许多业内人士错误地预测了成本削减的终结。从f16 / f14节点到i5 / f2.5节点,我们预计成本将以每节点0.72倍的速度降低,然后减速至每节点0.87倍。g1.25和g0.9节点分别是具有3个和4个堆叠层的通用CFET制程。
图11展示了掩模组摊销对晶圆成本的影响。
图11.掩模组摊销成本。
图11中的晶圆成本是基于台湾新建的晶圆厂,每月生产40,000片晶圆。摊销仅是掩模组,不包括设计成本。
该表列出了2020年250nm,90nm,28nm和7nm掩模组的掩模成本。请注意,这些掩模组在介绍时比较昂贵。掩模组成本是在一定数量的晶圆上摊销的,其标准化成本如图所示。在该表中,晶片成本比率是在掩模组上运行的100个晶片的摊销成本,除以在掩模组上运行的100,000个晶片的摊销成本。
从该图和表中,我们可以看到,掩模组摊销在250nm(比例为1.42x)时影响较小,而在7nm(比例为18.05x)时影响较大。设计成本摊销甚至更糟。最重要的是,设计和掩模组成本在先进节点是如此之高,以至于只有大批量产品才能吸收由此产生的摊销费用。
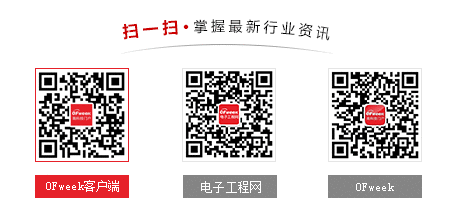
图片新闻
最新活动更多
-
即日-12.5立即观看>> 松下新能源中国布局:锂一次电池新品介绍
-
12月12日火热报名中>>> STM32全球线上峰会
-
即日-12.18立即报名>>> 【在线会议】Automation1微纳精密运动控制系统
-
12月19日立即报名>> 【线下会议】OFweek 2024(第九届)物联网产业大会
-
即日-12.26立即报名>>> 【在线会议】村田用于AR/VR设计开发解决方案
-
即日-12.26火热报名中>> OFweek2024中国智造CIO在线峰会
发表评论
请输入评论内容...
请输入评论/评论长度6~500个字
暂无评论
暂无评论