7.30-8.1 全数会2025(第六届)机器人及智能工厂展
火热报名中>>
波峰焊接孔孔铜缺失的失效机理简析
插件孔是实现PCB不同层线路互连的主要桥梁,因而其孔内铜层的完整性成为PCB备受关注的热点之一。一直以来,孔无铜的失效案例屡见不鲜,严重影响PCB的性能和可靠性。在焊接过程出现异常时,孔铜被锡溶蚀(浸析现象)是导致孔无铜的常见失效原因之一,目前有关此类失效案例的分析文章尚少,本文结合一例波峰焊后锡溶铜导致的孔无铜失效案例,对波峰焊后焊接面孔铜缺失的机理进行简析。
1 波峰焊接简介
波峰焊是指将熔化的软钎焊料,经电动泵或电磁泵喷流成设计要求的焊料波峰,亦可通过向焊料池注入氮气来形成,使预先装有元器件的印制板通过焊料波峰,实现元器件焊端或引脚与印制板焊盘之间机械与电气连接的软钎焊。
波峰焊的主要工艺流程:将元件插入相应的元件孔中→预涂助焊剂→预烘(温度90-100℃,长度 1~1.2m)→波峰焊(220-240℃)→切除多余插件脚→检查。
图1 波峰焊示意图
2 失效案例分析
2.1 案例背景
某PCB板在完成波峰焊后外观检查发现SS面(即波峰焊接起始面)整排1.5mm插件孔均出现缺失的现象,其余位置外观上锡良好,未发现孔环缺失现象,不良率为0.67%,其表面处理为有铅喷锡(HASL)。
不良板孔环缺失位置确认如图2所示:
通过立体显微镜观察PCB板不良位置的孔环情况,发现不良孔孔环位置无完整的铜层,部分位置已裸露出基材。
通过查找相关生产信息可知,该PCB板的生产流程包括化学沉铜、负片电镀(最小孔壁铜厚要求为20μm)、磨板、酸性蚀刻、有铅喷锡等。
2.2 失效模式分析及定位
根据该板的生产流程可知,可能导致孔环缺失的原因主要有:酸性蚀刻的药水对铜的咬蚀,有铅喷锡对铜的溶蚀和波峰焊接锡对铜的溶蚀等。现对不良板的孔环缺失位置和板上其它未进行波峰焊接的PTH孔进行垂直切片分析对比,如图3所示:
从图3可以看出,对于表面处理为有铅喷锡的PCB板,未进行波峰焊接的PTH孔的孔铜仅被喷锡过程咬掉4.4μm的厚度。而波峰焊后的PTH孔在波峰焊接起始面有孔环缺失的不良现象(如孔环缺失位置-2所示),焊接终止面孔环的孔铜完整,因而可以排除不良孔的孔铜缺失是由有铅喷锡对铜的溶蚀导致的。另外,在不良孔的孔口位置有部分铜残留,残留的铜层厚度为14.9μm,阻焊下的铜层完好无缺,厚度为46.6μm,说明在阻焊工序之前孔环位置孔环铜厚满足要求,可以排除不良孔的孔铜缺失是由酸性蚀刻过程中被药水咬蚀导致。因此,推断不良孔的孔环铜层可能是在后续进行波峰焊接时出现异常,导致铜被锡溶蚀的失效。
2.3 失效模式确认
为了进一步验证不良孔孔铜缺失的真因,现对失效孔环位置进行垂直切片分析,确认其失效模式,如图4所示:
不良孔的孔铜在波峰焊之后,沿着焊接起始面到终止面,孔铜由薄到厚渐变,孔环、孔口和内侧孔壁铜均被逐步溶蚀,且焊接起始面的孔环和孔口铜层优先被咬蚀干净,而孔内远离波峰面的孔环和孔壁铜则相对完整,被咬蚀掉的厚度较轻微。
2.4 孔铜的浸析机理简析
在焊接过程中,焊料处于熔融状态,浸入熔融焊料的PCB板的铜会向锡中扩散和溶解,在生产中将这种现象称为浸析现象或“溶蚀”现象。发生浸析现象的本质,是由于金属铜与液态焊料的金属锡之间存在着良好的亲和力。
波峰焊接所采用的焊料分为有铅和无铅焊料,在各种焊料中Sn都是主要成分,铜在锡的溶解率取决于许多因素:焊接时的温度、焊料成分,以及焊接时间和焊料的流动速度等。在生产过程中,这些参数异常可能会导致孔铜被锡溶蚀的不良现象。
3 改善建议
铜在锡的溶解率取决于焊接时的温度、焊料成分,以及焊接时间和焊料的流动速度等因素。因此,可以通过以下方法控制铜的溶蚀程度:
(1)正确设置波峰焊的温度曲线,并通过定期检测实时温度曲线来调节温度曲线;
(2)适当缩短焊接时间,避免PCB板的铜长时间接触锡料;
(3)定期清理锡渣,加强设备的日常维护,让设备可以正常工作,防止出现卡板、波峰不均等现象。
4 结论
在波峰焊中,一些生产异常会导致PCB板的插件孔浸入锡料的时间过久,孔铜会被逐步浸析溶解,溶解在锡料的Cu随着时间的延长会越来越多,会导致锡料的黏度增加以及锡料熔点上升等问题。
在实际生产中,应规范操作,严格管控焊接温度和焊接时间等工艺参数,提升人员的操作技能等,防止PCB板在生产过程中出现孔铜溶蚀的失效现象。
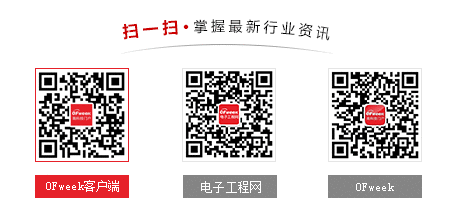
图片新闻
技术文库
最新活动更多
-
3月27日立即报名>> 【工程师系列】汽车电子技术在线大会
-
4月25日立即报名>> 【线下论坛】新唐科技2025新品发布会
-
在线会议观看回放>>> AI加速卡中村田的技术创新与趋势探讨
-
4月30日立即参与 >> 【白皮书】研华机器视觉项目召集令
-
即日-5.15立即报名>>> 【在线会议】安森美Hyperlux™ ID系列引领iToF技术革新
-
5月15日立即下载>> 【白皮书】精确和高效地表征3000V/20A功率器件应用指南
推荐专题
发表评论
请输入评论内容...
请输入评论/评论长度6~500个字
暂无评论
暂无评论