7.30-8.1 全数会2025(第六届)机器人及智能工厂展
火热报名中>>
电子微组装技术发展历程及特点
二、电子微组装技术发展历程及特点
作为电子组装封装技术的组成部分,电子微组装技术以传统电子封装技术为基础,为适应产品微型化的需求而得以不断发展。产业化的电子组装封装技术发展至今,已有60多年的历史。
1.电子组装封装技术发展历程
20世纪50年代,电子元器件主要有真空电子管、长引脚无源元件,这时通常采用导线连接、螺丝拧紧的方式在金属板框架上固定元器件,并未形成或提出组装密度的概念。应用的代表产品有电子管收音机。
20世纪60年代,半导体晶体管的出现,逐步取代了真空电子管,开始使用轴向引线元件和晶体管,采用手工焊接工艺,将元器件引脚插入单面印制电路板(PCB)的焊孔进行焊接,实现了在PCB电路板上组装元器件,大大缩小了电子产品的体积。应用的代表产品有塑料外壳半导体收音机。
20世纪70年代,发展了以双列直插式封装(Double In-line Package, DIP)和插针网格阵列封装(Pin Grid Array Package, PGA)为代表的半导体集成电路(Integrated Circuit, IC),以及径向引脚的无源元件,采用自动插装技术在双面PCB电路板上组装元器件。应用的代表产品有黑白、彩色电视机。
20世纪80年代,发展了以四边扁平封装、四边J形引脚扁平封装为代表的大规模集成电路,形成标准化的表面贴装器件(Surface Mounted Device, SMD)和表面贴装元件(Surface Mounted Component, SMC),采用表面贴装技术(SMT)在多层布线PCB和多种陶瓷基板上组装元器件。应用的代表产品有电子表、电子照相机。
20世纪90年代,发展了以球栅阵列(Ball Grid Array, BGA)和芯片尺寸封装(Chip Size Package, CSP)为代表的高密度封装器件,以及超大规模半导体集成电路和多芯片组件(MCM),形成了封装、芯片面积比小于1.5的高封装效率技术,采用自动贴装技术在高密度多层PCB、玻璃基板(Chip on Glass, COG)和多层陶瓷基板上组装元器件或裸芯片。其中,MCM是在HIC基础上发展起来的用于高性能系统的模块产品,价格昂贵,主要应用于航天、航空等高性能、高可靠性要求的产品,如IBM 4300系列大型计算机系统的MCM结构CPU,其陶瓷基板有40多层,包含25种IC。其他商业化应用的代表产品有手机、便携式电子产品。
2000—2010年,发展了系统级封装(SiP)技术、圆片级封装技术(WLP),并形成实用化产品。SiP是在成熟的主流IC装配技术和表面安装技术(SMT)基础上发展起来的高密度封装新技术,充分利用现有成熟的组装技术,灵活运用各种不同芯片资源和封装互连优势,在保持SiP系统高性能的同时降低成本,其封装解决方案包括:芯片并列、堆叠结构,PoP封装结构,PiP封装结构。应用的代表产品有智能手机、迷你移动存储卡、蓝牙模块等。
2010年至今,开发了极小化元器件,组装在挠性带载基板(Flexible Printed Circuit, FPC)上,打造生活化可穿戴设备,其特点是:低功耗、低成本、小尺寸,应用的代表产品有与互联网结合的智能手环、手表、眼镜、衣服等可贴身穿戴的电子产品。同期,进一步发展了SiP和SoP系统集成技术,在SiP芯片级互连方面,为获得更高性能和组装密度,不断优化3D芯片堆叠和TSV硅通孔技术;在SoP多层基板互连和元器件组装方面,开发了内埋置元件多功能基板,SiP、SoP封装技术在射频和无线电设备、固体硬盘、汽车电子、微机电系统等领域的应用不断拓展。
国际半导体技术路线图(ITRS)报告(2015年)指出,半导体芯片体积到2021年将不再缩小,预测技术进步的传统“摩尔定律(Moore's Law)”—每1~2年单芯片内晶体管数量翻倍且性能提升一倍,将在5年内终结,如图2所示。为持续提高半导体器件性能和运算速度,芯片只能向3D转型,3D堆叠等新型微组装技术将在短期内成为芯片晶体管密度提高的重要手段,并被解释为预测技术进步的“摩尔定律升级(More than Moore)”,在“ITRS 2.0”中,3D集成技术将聚焦系统集成、异构集成和异构组成等三维集成微组装技术。长远来看,多种功能芯片的高密度集成必然带来新型电子微组装技术的发展和革命。
图2 ITRS报告:传统“摩尔定律”将在2021年终结
2.电子微组装技术发展趋势和特点
自1960年出现晶体管以来,电子封装50多年的演变和发展趋势如图3所示。
图3 电子封装50多年的演变和发展
与SiP相比,SoP亦是系统级封装的概念,虽然都采用“封装”来描述,但前者强调一个小型完整“封装”的理念,后者强调在单一基板上实现系统功能“组装”的理念,各有优势和适用范围。为保证系统级封装的一体化,SiP注重芯片级互连技术,通过芯片叠层、硅TSV通孔、芯片倒装焊和内引线键合等互连技术,实现对构成系统功能的各类裸芯片在单一封装体内的高密度组装,系统功能的拓展则采用PoP或PiP封装技术,SiP大量应用于存储器等数字产品和高可靠性产品。而为保证复杂系统功能在单一基板上的实现,SoP注重无源嵌入及多层布线基板技术,通过LTCC、MLCC、厚膜等多层布线基板技术和可埋置薄膜阻容感元件技术,实现对构成系统功能的各类独立封装元器件(包括MCM、SiP)在单一多功能基板上的高密度组装,以满足各种复杂系统功能的组装要求,SoP主要应用于射频/微波组件、光学探测和微机电传感等微系统产品。从近10年的系统级封装技术发展和应用对比来看,SiP商业化产品已成熟推出,而SoP的更高性能的多层基板技术还在不断开发和完善,其成熟的商业化产品仍在期待中。
为适应电子产品的小型化应用,21世纪初至今,电子微组装技术在三个方向不断创新和进步。
(1)微米级的组装技术,实现更小尺寸、更高密度的封装。如:硅芯片TSV通孔技术、碳纳米管微凸点技术。
(2)圆片级封装(Wafer Level Package, WLP)技术,实现工艺成本的降低和封装效率及可靠性的提高。如:从Fan-in WLP发展到Fan-out WLP,通过eWLP-BGA结构使3D SiP封装在纵向互连。
(3)满足系统功能的3D封装物理布局设计技术,以最合理的封装结构实现产品的系统功能。如:通过基于SiP的信息安全芯片集成设计技术解决信息安全系统中逻辑芯片与存储器难集成的问题,采用内埋置多层布线基板和芯片叠层组装技术满足射频收发及D/A转换等系统功能设计要求,采用单晶硅基板和硅埋置型多层BCB/Au布线的SiP封装工艺技术满足k波段雷达功分器的设计要求,利用多层厚膜布线基板技术设计以满足毫米波SoP电路系统功能,以及利用先进的埋置型晶圆级BGA技术和PoP技术(eWLB-PoP)解决手机高密度封装问题并满足相应的功能要求。实际上,系统级封装(SiP、SoP)的设计,需要综合考虑产品的功能、尺寸、重量、成本和可靠性要求,是需要将产品功能与传统PCB技术、先进SoC及SiP/SoP互连技术协同设计的封装技术。
ITRS报告关于3DIC TSV的技术路线图表明,2009—2015年,TSV技术进步特点是尺寸减小到原来的一半,见表1;ITRS报告关于SiP芯片与基板布线互连的丝键合水平,见表2。
表1 ITRS 3DIC TSV路线图:TSV技术
注:W2W,Wafer to Wafer,晶片与晶片(堆叠);
D2W,Die to Wafer,芯片与圆片(堆叠);
D2D,Die to Die,芯片与芯片(堆叠);
TSV,Through Silicon Via,硅通孔。
表2 ITRS关于SiP封装的丝键合水平
总体而言,随着电子封装技术的快速发展,特别是电子微组装技术的加入和拓展,半导体技术、封装技术和系统级封装产品之间不断渗透,界限越来越模糊。在一个系统级封装产品中,由于元器件高密度组装,其微组装材料既是结构的固定材料又是电路的阻容感元件,特别是微波电路产品,因此系统功能的实现与半导体裸芯片之间的互连方式以及多层基板布线结构的设计直接相关。
从产品的角度,在电子微组装技术创新和进步的带动下,电子封装技术有以下八个主要发展方向:
① 向着高密度、多I/O数方向发展;
② 向着提高表面贴装密度方向发展;
③ 向着高频、大功率方向发展;
④ 向着薄型化、微型化、不对称化、低成本化方向发展;
⑤ 从单芯片封装向多芯片封装发展;
⑥ 从2D平面封装向3D立体封装方向发展;
⑦ 向着系统级封装(SiP、SoP)方向发展;
⑧ 向着绿色环保化方向发展。
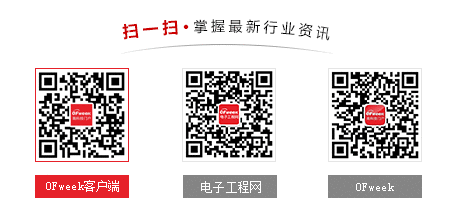
图片新闻
技术文库
最新活动更多
-
3月27日立即报名>> 【工程师系列】汽车电子技术在线大会
-
4月1日立即下载>> 【村田汽车】汽车E/E架构革新中,新智能座舱挑战的解决方案
-
即日-4.22立即报名>> 【在线会议】汽车腐蚀及防护的多物理场仿真
-
4月23日立即报名>> 【在线会议】研华嵌入式核心优势,以Edge AI驱动机器视觉升级
-
4月25日立即报名>> 【线下论坛】新唐科技2025新品发布会
-
4月30日立即参与 >> 【白皮书】研华机器视觉项目召集令
推荐专题
发表评论
请输入评论内容...
请输入评论/评论长度6~500个字
暂无评论
暂无评论